Infrastructure
Manufacturing
Our infrastructure is spread over a large area and is divided into number of units such as manufacturing unit, designing and quality testing unit. Our manufacturing unit is equipped with all the necessary machines and equipment required for the production of Railway light fittings and components.
We use following machines & equipment in our infrastructure:
-
Injection Molding Machine
-
Vertical Injection Molding Machine
-
Ultra Sonic Welding Machine
-
Drill Machine
-
Revitting Machine
-
Terminal Machine
Production Planning & Quality Control.jpg)
Production planning and Control department is one of the important department for the apparel manufacturing company. In the context of the apparel manufacturing primary roles of the Production Planning and Control (PPC) department has been listed below. Each functions has been explained briefly just overview about the task. To know details about the task read related articles.
Material Resource Planning (Inventory): Preparation of Material requirement sheet according to sample product and buyer specification sheet. Consumption of material (fabric, thread, button, and twill tape) is calculated and estimated cost of each material.
Loading production: Planner defines which style to be loaded to the production line and how much quantity to be loaded.
Process selection & planning: Processes needed to complete an order vary style to style. According to the order (customer) requirement PPC department select processes for the orders. Sometime extra processes are eliminated to reduce cost of production.
Facility location: Where a company has multiple factories (facilities) for production and factories are set for specific product, planner need to identify which facility will be most suitable for new orders. Sometimes there may be a capacity shortage in a factory, in that case planner need to decide which facility will selected for that orders.
Estimating quantity and costs of production: Planner estimate daily production (units) according to the styles work content. With the estimated production figure, production runs and manpower involvement planner also estimate production cost per pieces.
Capacity planning: PPC department plays a major role during order booking. They decide (suggest) how much order they should accept according to their production capacity. Allocating of total capacity or deciding how much capacity to be used for an order out of total factory capacity. Regularly updating factories current capacity (production capacity).
Reasearch & Development 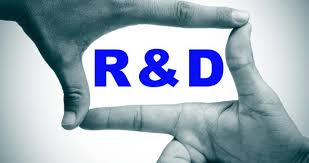
We have set up a separate department of research and development to offer products in accordance with changing market needs. This department is managed by an expert team of researchers who conduct several research activities to find out the most cost effective method of manufacturing light fittings and components. These researchers often come out with innovative and new ideas which help us to upgrade our existing range of products. Further, they maintain a documented research of their researches for any future reference.
Owing to our intensive research process, we often find best solution to the client’s problems and recognized as trusted manufacturers of light fittings and components.
New Product Research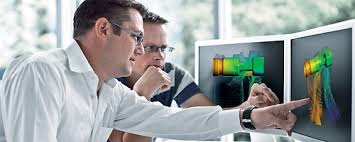
Before a new product is developed, a research and development department conducts a thorough study to support the project. The research phase includes determining product specifications, production costs and a production time line. The research also is likely to include an evaluation of the need for the product before the design begins to ensure it is a functional product that customers want to use.
New Product Development.jpg)
The research paves the way for the development phase. This is the time when the new product is actually developed based on the requirements and ideas created during the research phase. The developed product must meet the product guidelines and any regulatory specifications.
Existing Product Updates
Existing products of the company also fall under the scope of research and development. The department regularly evaluates the products offered by the company to ensure they are still functional. Potential changes or upgrades are considered. In some cases, the research and development department is asked to resolve a problem with an existing product that malfunctions or to find a new solution if the manufacturing process must change.
Quality Checks
In many companies, the research and development team handles the quality checks on products created by the company. The department has an intimate knowledge of the requirements and specifications of a particular project. This allows team members to ensure the products meet those standards so the company puts out quality products. If the company also has a quality assurance team, it may collaborate with research and development on quality checks.
Innovation
The research and development team aids the company in staying competitive with others in the industry. The department is able to research and analyze the products other businesses are creating, as well as the new trends within the industry. This research aids the department in developing and updating the products created by the company. The team helps direct the future of the company based on the information it provides and products it creates.
Purchasing
.jpg)
Most major companies and even some government organizations have a purchasing or procurement department as part of everyday operations. These departments provide a service that is the backbone of many manufacturing, retail, military and other industrial organizations. Many individuals, even some who work for these companies, are unaware of what the purchasing department does, why it exists or what purposes it serves. To understand better what the role of the purchasing department is, consider some functions it performs.
Procuring Materials
One role of the purchasing department is to procure all necessary materials needed for production or daily operation of the company or government organization. For a manufacturing company, this might include raw materials such as iron, steel, aluminum or plastics, but it also might include tools, machinery, delivery trucks or even the office supplies needed for the secretaries and sales team. In a retail environment, the purchasing department makes sure there is always sufficient product on the shelves or in the warehouses to keep the customers happy and keep the store well-stocked. With a small business, it is especially important to keep inventory ordering at a reasonable level; investing large amounts of capital in excess stock could result in storage problems and in a shortage of capital for other expenditures such as advertising or research and development. Purchasing also oversees all of the vendors that supply a company with the items it needs to operate properly.
Evaluating Price.jpg)
A purchasing department also is charged with continuously evaluating whether it is receiving these materials at the best possible price in order to maximize profitability. This can be challenging for a small business that may purchase in lesser quantities than a larger vendor and which thus may not receive the same type of bulk discounts. A purchasing department in a small business needs to shop around to find the best vendors at the most reasonable prices for the company's particular size orders. Purchasing department staff may communicate with alternate vendors, negotiate better pricing for bulk orders or investigate the possibility of procuring cheaper materials from alternative sources as part of their daily activities.
Paper Work and Accounting
Purchasing departments handle all of the paperwork involved with purchasing and delivery of supplies and materials. Purchasing ensures timely delivery of materials from vendors, generates and tracks purchase orders and works alongside the receiving department and the accounts payable department to ensure that promised deliveries were received in full and are being paid for on time. In a small business, this means working closely with the accounting department to ensure that there is sufficient capital to buy the items purchased and that cash is flowing smoothly and all payments are made on time.
Policy Compliance
The purchasing department also must ensure that it is complying with all company policies. For example, in a small business, individual staff members may communicate with the purchasing department about purchasing needs for things such as office supplies or computers. Before making a purchase, the purchasing department must ensure that it heeds the proper protocols for purchase and budget approval and must ensure that any items are purchased in accordance with the overall purchasing policy of the organization.
Client Satisfaction 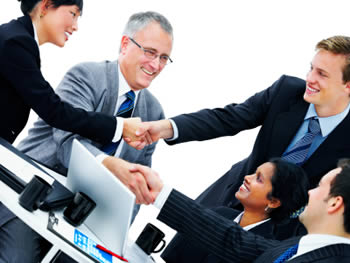
Client satisfaction is our foremost goal therefore; we strive to offer quality range of light fittings and components. Our range is manufactured using modern technology and quality raw materials which ensure low energy consumption and optimum performance. As we assure that the products are delivered on time, our clients
Owing to our vast industrial experience we have been able to meet the exact requirements of railway and automobile industry. Our client centric approach has enabled us to secure a huge client base not only in India but in many other countries.